Screw-in undercut anchors are a sophisticated and reliable fastening solution, especially valued in construction for their high performance in demanding applications. This guide will delve into their mechanics, installation, performance, and optimal use cases.
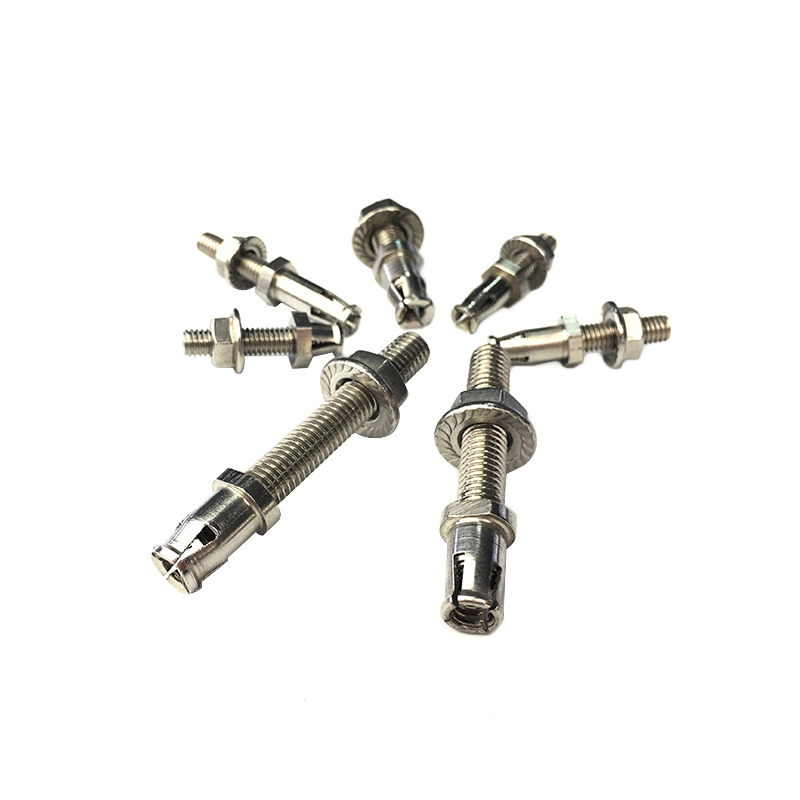
A screw-in undercut anchor is a mechanical anchor that creates an interlock with the base material by forming an "undercut" profile within the drilled hole. Unlike expansion anchors that rely on friction, undercut anchors derive their holding power from a positive mechanical connection.
Structure and Working Principle
The anchor typically consists of a threaded rod or screw with a specialized tip and a matching sleeve or expansion element. During installation, a pre-drilled hole is created, often with a pilot drill followed by an undercutting tool. When the anchor is screwed into the hole, the tip expands or cuts into the base material, creating a reverse-cone shape or an "undercut." This unique shape locks the anchor into the concrete or masonry, providing exceptional resistance to pull-out loads.
Applicable Materials
Screw-in undercut anchors are primarily designed for use in dense, solid materials. They are most commonly used in concrete (both cracked and uncracked) and certain types of masonry. Their design makes them particularly effective in applications where the integrity of the base material is critical.
Comparison with Other Anchors
- Wedge anchors: These are expansion anchors that rely on friction. While effective for many applications, they can exert significant stress on the base material and are less suitable for dynamic loads or close-edge installations compared to undercut anchors.
- Drop-in anchors: These are also expansion anchors, typically used for lighter loads. They offer less pull-out strength than screw-in undercut anchors and are not generally recommended for heavy-duty or seismic applications.
- Screw-in undercut anchors offer superior performance in terms of load capacity, reduced edge distance requirements, and suitability for dynamic and seismic loads due to their positive mechanical interlock.
How to Install a Screw-In Undercut Anchor
Proper installation is crucial to ensure the optimal performance of a screw-in undercut anchor.
Required Tools
- Rotary hammer drill: For creating the initial pilot hole.
- Undercutting drill bit: A specialized bit designed to create the undercut profile at the bottom of the hole.
- Hole cleaning tools: Brush and vacuum to remove debris from the drilled hole.
- Torque wrench: To ensure the anchor is tightened to the manufacturer's specified torque.
Step-by-Step Installation Guide
- Drill the pilot hole: Using the rotary hammer drill, create a pilot hole to the specified depth.
- Clean the hole: Thoroughly clean the hole using a brush and vacuum to remove all dust and debris. This is critical for the undercut to form correctly.
- Create the undercut: Insert the specialized undercutting drill bit and operate the drill according to the manufacturer's instructions to create the undercut profile.
- Clean the hole again: Repeat the cleaning process to ensure no debris remains from the undercutting process.
- Screw in the anchor: Insert the screw-in undercut anchor into the prepared hole and tighten it with a torque wrench to the recommended torque value. As the anchor is tightened, its design engages with the undercut, creating the mechanical interlock.
Common Installation Mistakes and How to Avoid Them
- Improper hole cleaning: Dust and debris can prevent the undercut from forming properly, significantly reducing the anchor's load capacity. Always clean the hole thoroughly.
- Incorrect drill bit size or type: Using the wrong drill bit or not using an undercutting bit will compromise the anchor's performance. Always use the manufacturer-specified tools.
- Over- or under-torquing: Applying too much or too little torque can lead to anchor failure. Use a calibrated torque wrench and adhere to the specified torque values.
Screw-In Undercut Anchor Load Capacity & Performance
The performance of screw-in undercut anchors is a key reason for their widespread use in critical applications.
Static and Dynamic Load Capacity
Screw-in undercut anchors boast excellent static load capacity, meaning they can withstand significant constant forces without deformation or failure. Furthermore, their mechanical interlock makes them highly resistant to dynamic loads, such as vibrations or repeated stresses, where other anchor types might fail due to fatigue. The screw-in undercut anchor wind load capacity is also a critical consideration for outdoor applications, particularly for facade systems and solar panel mounting, where they must withstand significant uplift and lateral forces.
Seismic Performance
One of the most significant advantages of screw-in undercut anchors is their seismic performance. They are often designed and tested to meet stringent requirements for seismic retrofitting and use in seismic zones. Their ability to resist significant movement and maintain integrity during seismic events makes them a preferred choice for critical infrastructure.
Temperature and Environmental Impact on Performance
Environmental factors can affect anchor performance. The screw-in undercut anchor fire resistance rating is an important consideration in buildings where fire safety is paramount. Anchors made of carbon steel will lose strength at elevated temperatures, while stainless steel options offer better performance in such conditions. Additionally, the screw-in undercut anchor corrosion resistance is vital for long-term durability, especially in corrosive environments or outdoor applications. Stainless steel anchors are generally preferred in such conditions.
Best Application Scenarios
The superior performance of screw-in undercut anchors makes them ideal for a wide range of demanding applications.
- Heavy-duty machinery: For anchoring heavy equipment that generates vibrations or requires extremely secure fastening.
- Overhead installations: Their reliable pull-out strength makes them perfect for suspending pipes, ducts, or other elements from ceilings.
- Seismic zones: As mentioned, their seismic resistance makes them invaluable in areas prone to earthquakes.
- Screw-in undercut anchor for facade systems: Their ability to handle significant loads and their discreet installation make them suitable for securing architectural facades.
- Screw-in undercut anchor for solar panel mounting: They provide robust and secure fastening for solar panel arrays, ensuring stability against wind uplift and other environmental forces.
- Screw-in undercut anchor for steel structures: They can be used to anchor steel elements to concrete foundations or other concrete components.
- Screw-in undercut anchor in precast concrete: Their precise installation and high performance make them suitable for securing elements within or to precast concrete components.
How to Choose the Right Screw-In Undercut Anchor?
Selecting the correct screw-in undercut anchor is essential for safety and performance.
Key Selection Factors
- Diameter and length: These depend on the load requirements and the thickness of the base material and the fixture being attached.
- Material:
- Carbon steel: Typically galvanized or zinc-plated for corrosion protection, suitable for dry, indoor environments.
- Stainless steel: Offers superior screw-in undercut anchor corrosion resistance, making it ideal for outdoor, corrosive, or damp environments.
- Load requirements: Always select an anchor with a safe working load capacity that exceeds the anticipated static and dynamic loads.
- Base material type: Ensure the anchor is approved for use in the specific concrete or masonry type you are working with.
How to Determine Quality
Look for anchors that meet recognized international standards and certifications. Key certifications include:
- ETA (European Technical Assessment): Indicates compliance with European standards for construction products, often including specific assessments for cracked concrete and seismic performance.
- ICC-ES (International Code Council Evaluation Service): Provides evidence that a product complies with building codes in North America.
These certifications ensure that the anchor has undergone rigorous testing and meets specific performance criteria, giving you confidence in its quality and reliability.
Contact Us